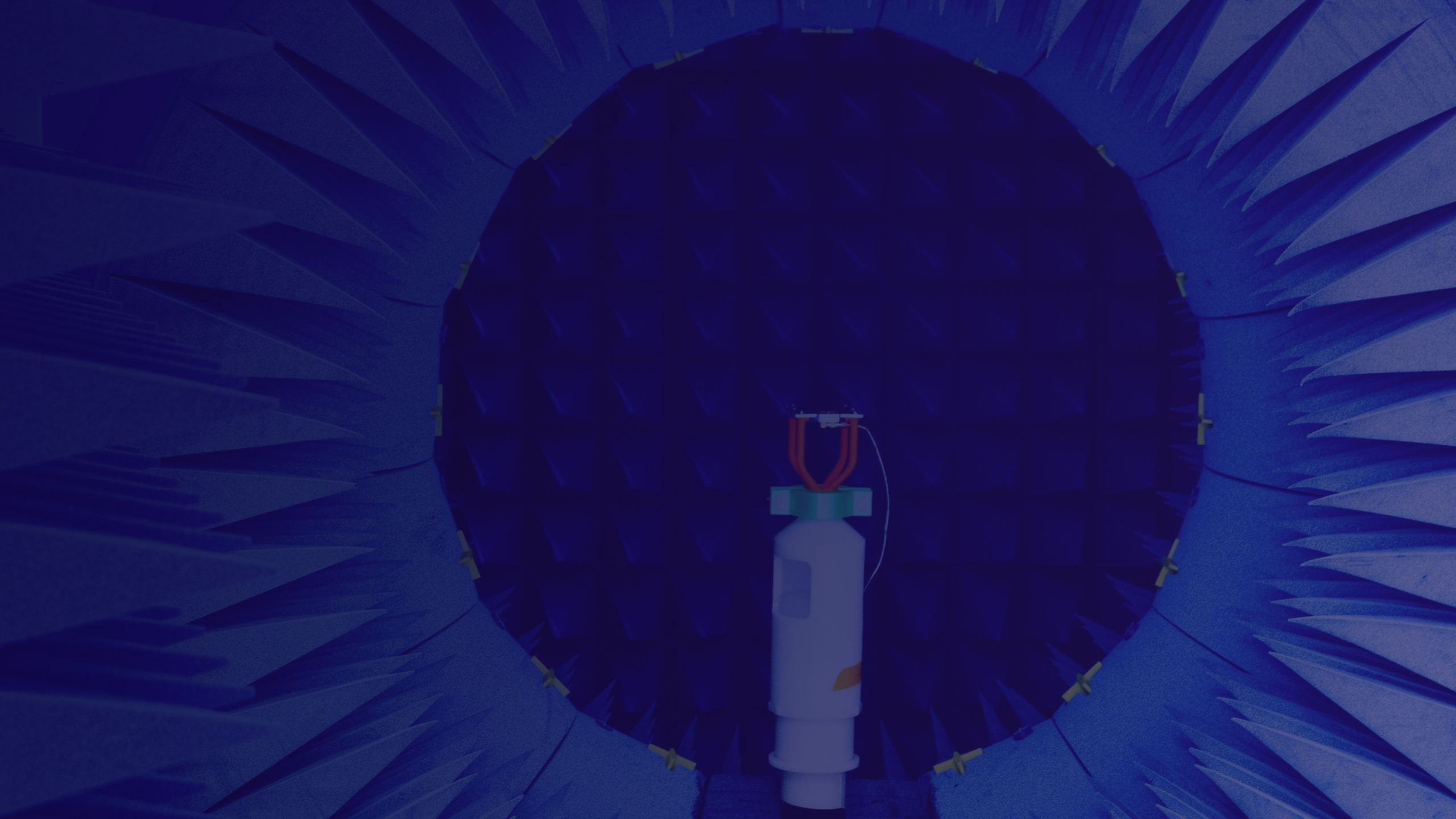
Our Testing Process:
The Pinnacle
of Quality and Rigor
Why trusting us for your Antenna Testing?
Number of Tests
Our testing process includes more tests than the industry average, increasing confidence in product reliability.
Quality and Rigor
We delve deeper into each test, applying a rigorous methodology to uncover even the most elusive issues.
Test Traceability
Every qualification test is meticulously recorded, and each acceptance test is detailed in a report included in the EIDP, offering unmatched transparency and traceability.
Reports automated with Connektica
Thanks to our partnership with Connektica, Anywaves can provide automated generated report for each flight model.
This report includes pictures and results of each test performed and it will be delivered alongside the antenna.
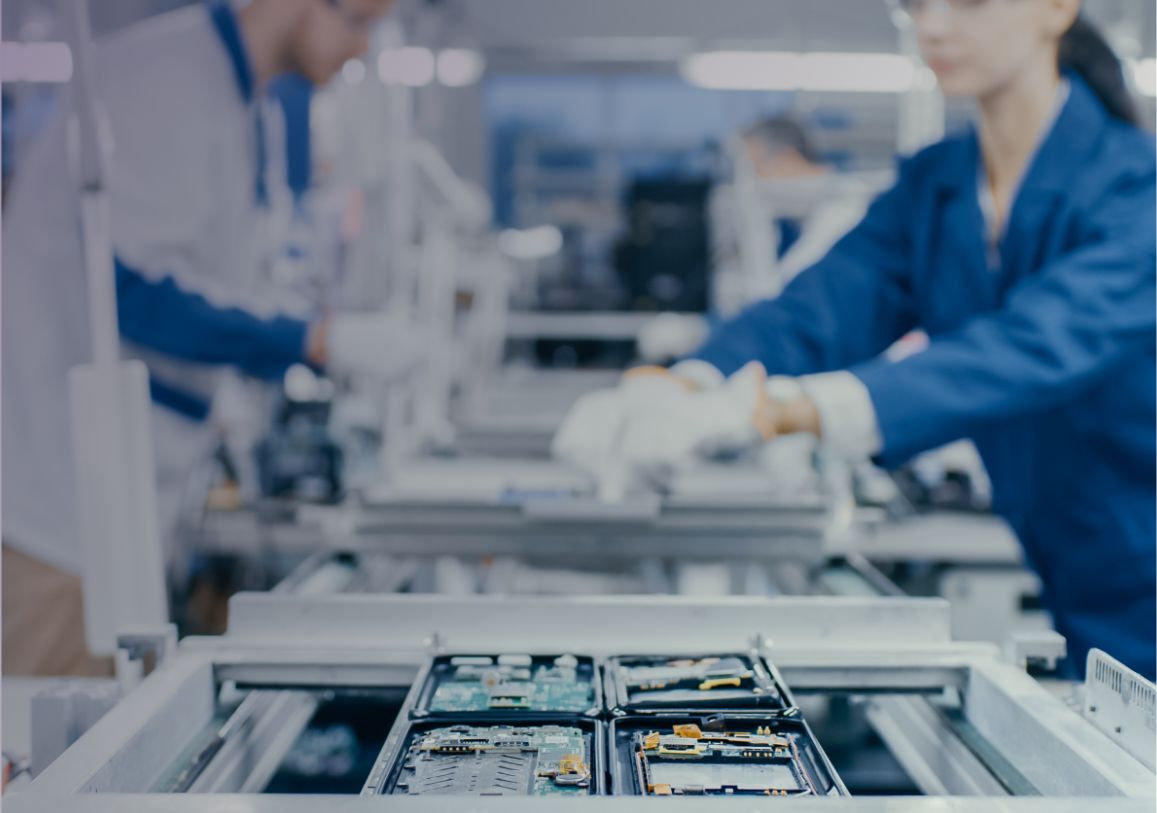
A Lean-Inspired Industrialization Process
We’ve infused lean manufacturing principles into our rigorous testing process, ensuring both efficiency and precision. Our meticulous and standardized testing protocols, paired with automated reporting, ensure that every antenna we produce undergoes consistent, uniform, and detailed evaluations.
This lean-inspired approach not only guarantees the reliability and quality of each antenna but is also optimized for high-volume industrialization, ensuring every product meets our exacting standards regardless of order size.
Custom Testing Solutions
Recognizing the ever-evolving challenges and requirements of space missions, Anywaves offers additional or specific tests upon request. We have partnerships with top-notch testing facilities and specialists, making us capable of performing any type of test you may need.
Whether it’s a unique environmental condition or a specific functional criterion, our network and expertise ensure that your unique testing requirements will be thoroughly addressed.
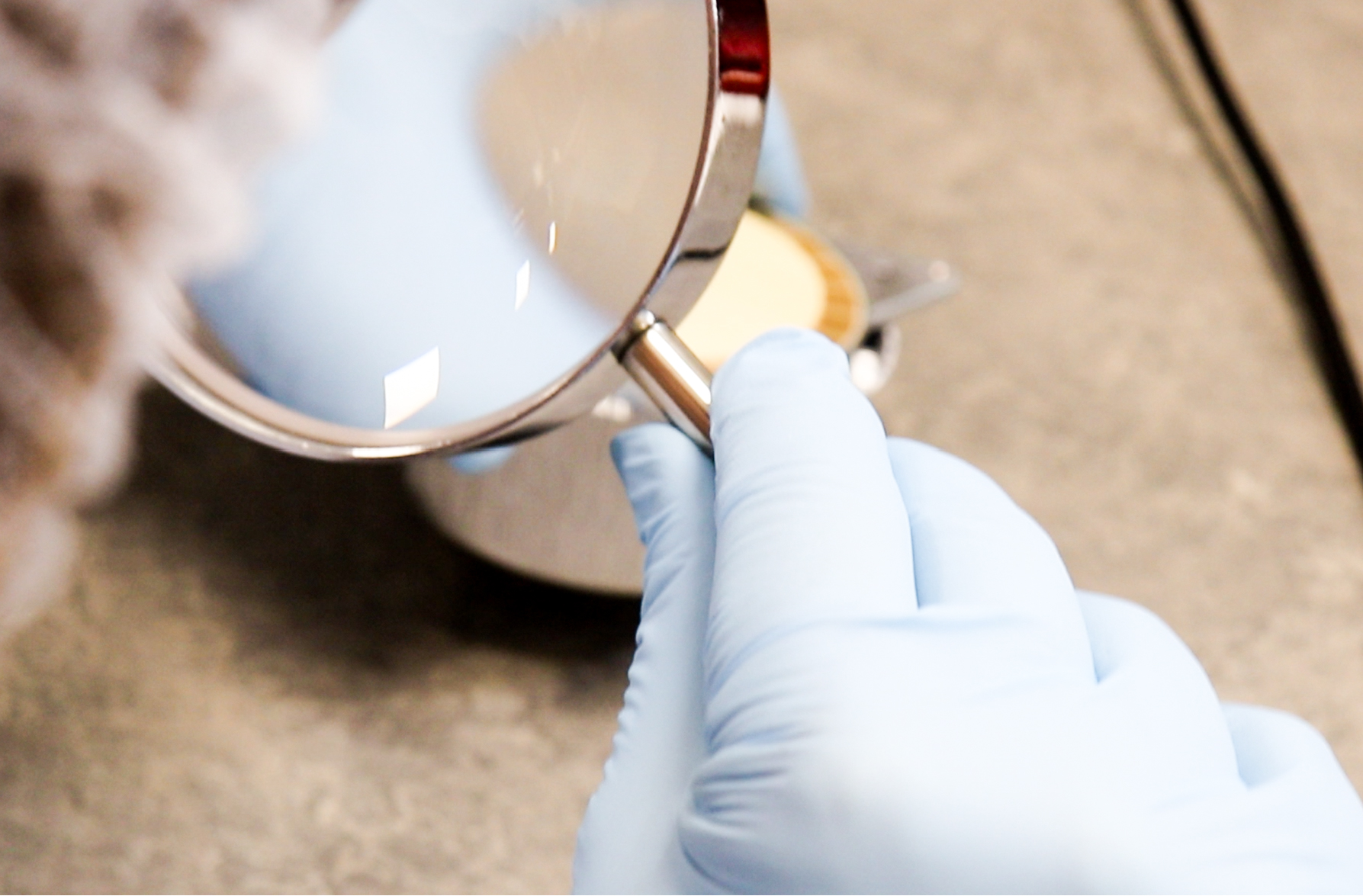
Introducing Our Test Caps
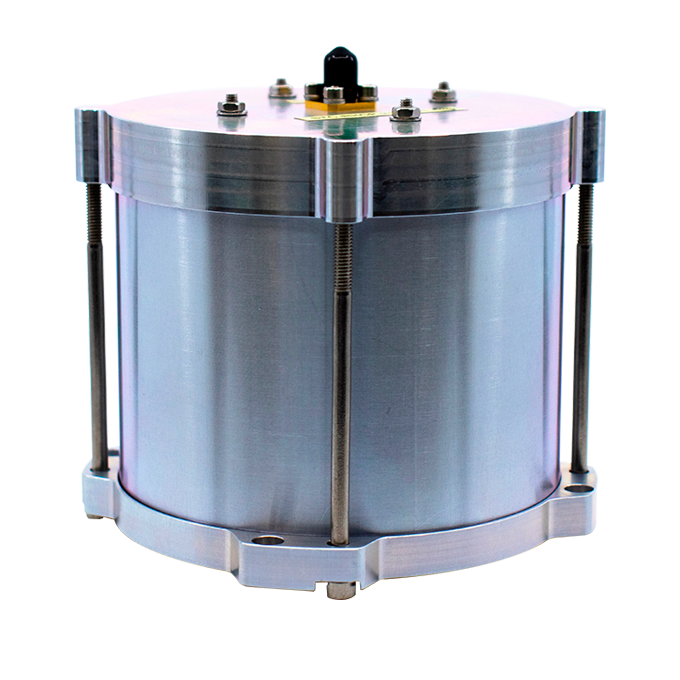
Specifically designed for comprehensive RF (Radio Frequency) tests on spatial antennas, our Test Caps (or Test hats) allow you to seamlessly conduct your own supplementary testing, ensuring your antennas function flawlessly.
These tools enable you to bypass the expensive and intricate procedures traditionally carried out in anechoic chambers. Not only do they streamline the testing process, but our Test Caps also guarantee safety, ensuring there’s minimal risk of damaging your antenna during evaluations.
By merging efficiency, reliability, and cost-effectiveness, our Test Caps represent a transformative shift in antenna testing methodology.
Resources
How Can We Help?
We look forward to hearing from you