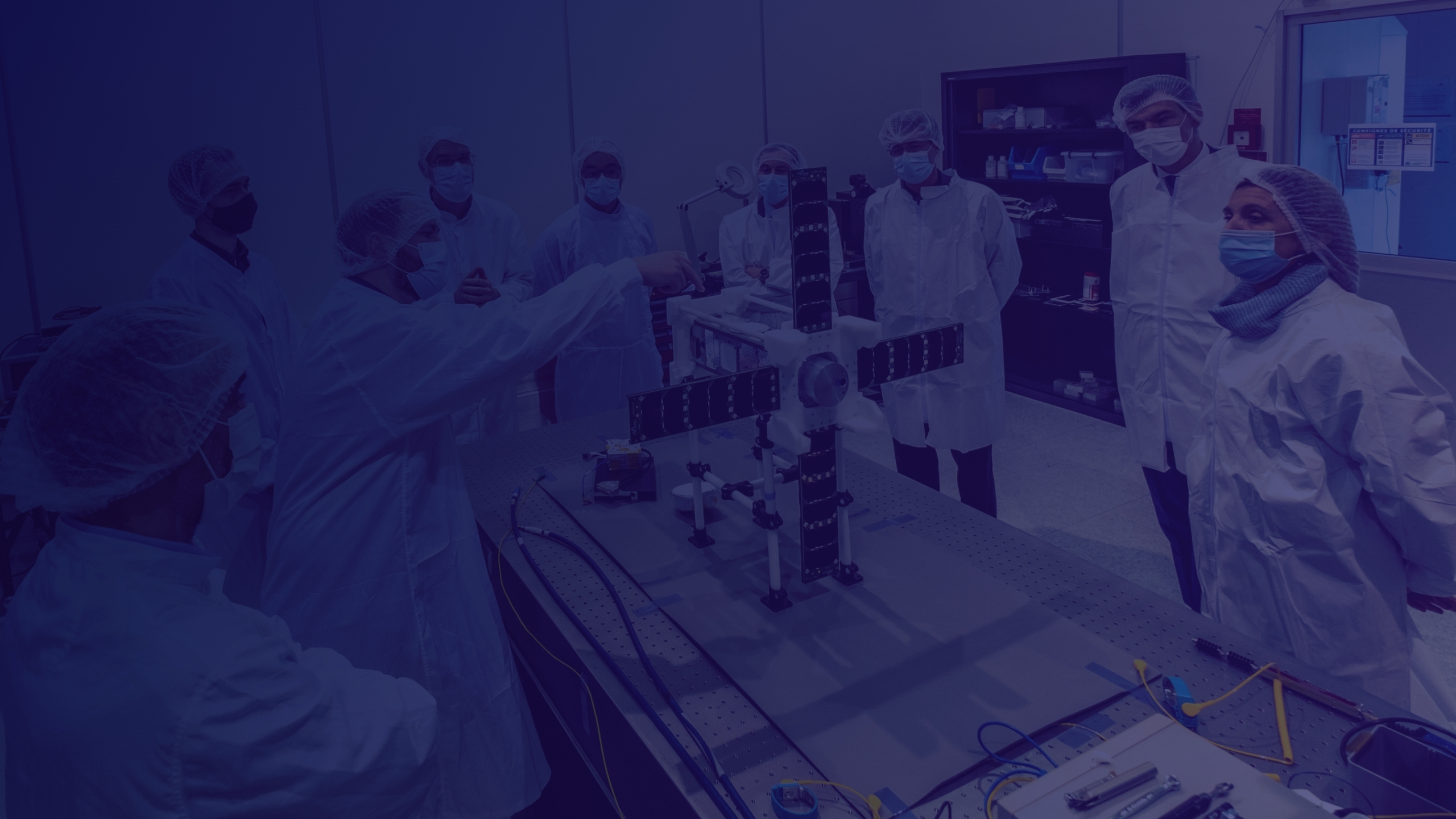
Our Quality Management Process:
Precision, Compliance,
and Dedication
A structured approach
- GAP ANALYSIS
We first identify gaps in our existing processes that could affect the quality of our space antennas. - SET OBJECTIVES
Specific, measurable, achievable, relevant, and time-based (SMART) objectives are set to guide the process improvement. - DEVELOP ACTION PLANS
Our teams outline the steps required to achieve these objectives, including the allocation of resources and setting of timelines. - CUSTOMER REQUIREMENTS
Special emphasis is placed on planning to ensure all processes and outcomes align with customer requirements, ensuring that the final product will meet their specific needs and expectations.
- IMPLEMENT CHANGES
Changes are applied on a small scale initially to test their effectiveness
- MONITOR PERFORMANCE
Using real-time data and key performance indicators (KPIs), we closely monitor the process to ensure that it’s working as planned. - REVIEW RESULTS
Data is analyzed and compared against the set objectives to evaluate the success of the action plans. - MAKE ADJUSTMENTS
Where necessary, immediate corrections are made to rectify any deviations from the desired outcome. - VALIDATE ANTENNA QUALITY
Before shipping, every aspect of our antennas, including documentation, meca-thermal and RF testing, and packaging, is thoroughly validated to ensure they meet our high standards.
- STANDARDIZE SUCCESS
If the changes result in an improvement, the new methods are standardized and applied across the board.
-
LOOP BACK
The cycle does not end here; we revisit the plan to identify new opportunities for improvement, making the PDCA cycle a continuous loop of quality control and enhancement.
The EN 9100 Standard
Our operations are EN 9100 certified, a rigorous aerospace quality standard that supersedes the ISO 9001 requirements. In practical terms, this impacts every aspect of our antenna production:
Material Traceability
From sourcing to production, every material used is meticulously tracked and documented.
Process Control
Strict protocols govern each production step, ensuring repeatability and eliminating deviations.
Product Validation
Rigorous functional and environmental tests, consistent with space qualifications, are performed on each antenna model.
Documentation
Every single operational and quality parameter is documented in compliance with EN 9100, ensuring full traceability and auditability.
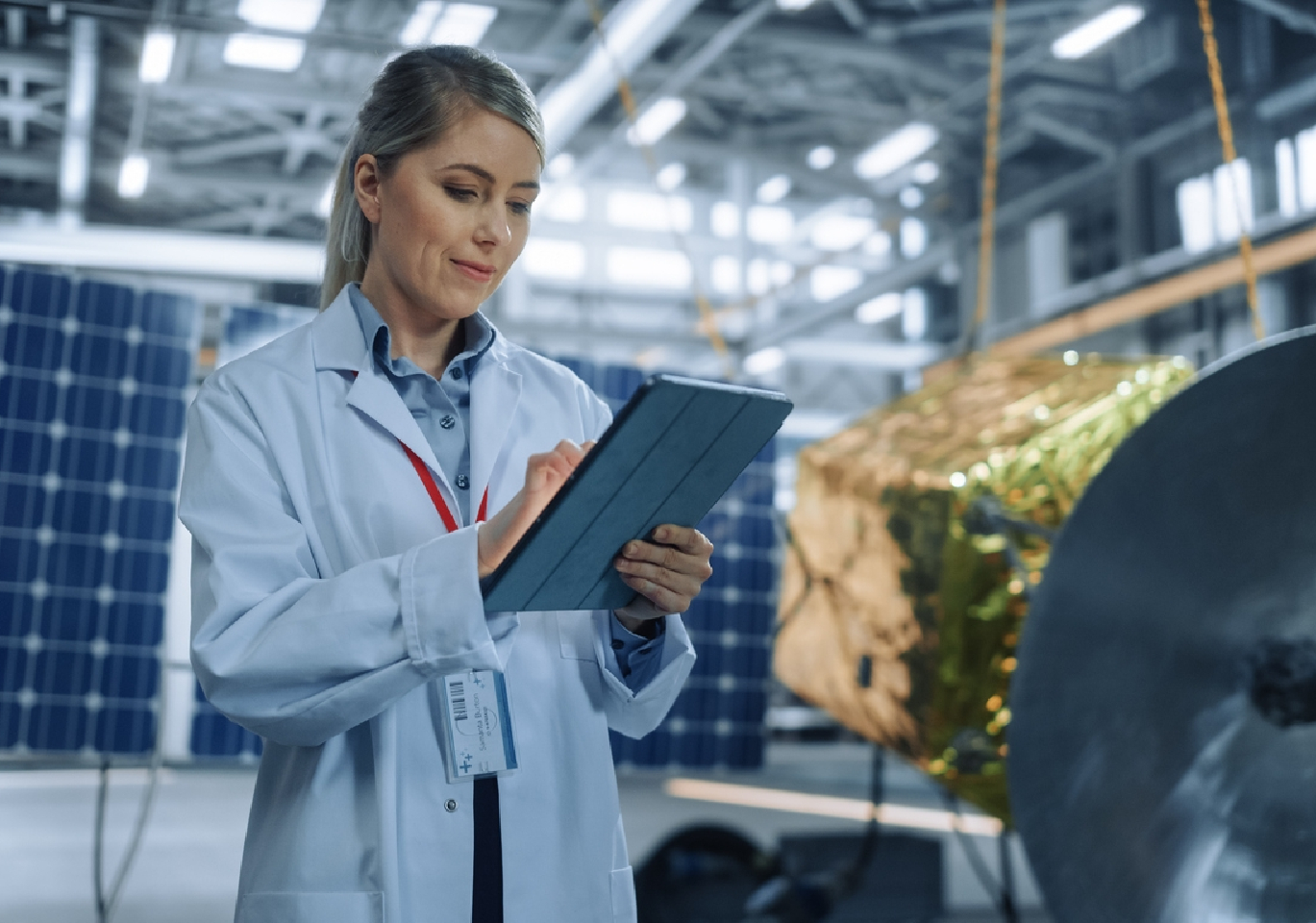
Managing Non-Conformities: Control, Anticipation, and Resolution
We understand that the nature of space missions leaves no room for errors. That’s why our quality management system is geared towards not just preventing, but also quickly identifying and rectifying any non-conformity. Our procedures for handling non-conformities involve:
As soon as a non-conformity is detected, the internal NRB (Non-Conformity Review Board) investigates the causes and consequences of the Non-Conformity and classifies the Non-Conformity either as minor or major. Immediate steps are taken to control the situation and prevent any adverse impact.
Through 8D approach, the root cause of the non-conformity is identified to prevent future occurrences.
Strategic corrective actions are implemented and monitored for effectiveness.
Every incident of non-conformity is thoroughly documented, and corrective actions are reviewed during our regular quality assessments.
Commitment to Continuous Improvement
We collectively commit to a continuous improvement approach. We continually refine our processes, tools, and management systems to ensure we’re delivering the best products to our customers.
We achieve this through:
To ensure that all processes meet or exceed industry standards.
Continual professional development to keep our team up-to-date with the latest best practices.
Active solicitation and rigorous analysis of customer feedback to inform product and process improvements.
How Can We Help?
We look forward to hearing from you