Launch, Land, Repeat: the rise of Reusable Rockets
Few developments in the past decade have reshaped the space industry as visibly as reusable rockets. Historically, rocket stages were designed for single-use: they blasted off, propelled payloads into orbit, then fell back to Earth or burned up on reentry—rarely to be seen again. This expendable model did the job, but at tremendous expense, both financially and environmentally. Today, however, that reality is changing. Multiple aerospace companies and space agencies are proving that refurbishing and reflying boosters can drastically cut launch costs and reduce waste, signaling a future where frequent and affordable launches are the new normal.
In this article, we’ll trace the evolution of reusable launchers, examining four key areas:
- The origins of reusability in rocketry and why it’s become a game-changer.
- The core technologies—landing systems, durable engines, and advanced materials—that make repeated flights viable.
- The challenges and opportunities that lie ahead, illustrated by real-life examples like the CALLISTO demonstrator.
- The critical role of launcher antennas in ensuring reliable communications, navigation, and control.
By exploring these topics, we gain a clearer sense of how the space industry is transitioning from an era of “launch and discard” to one of reuse and sustainable growth. Whether you’re a satellite manufacturer seeking cheaper access to orbit, a space enthusiast following the latest rocket landings, or an engineer delving into flight control systems, reusability has implications for everyone who cares about Earth-to-orbit missions.
The Emergence of Reusable Rockets
Early Efforts and the Rise of a New Paradigm
For much of the 20th century, orbital launches were rooted in ballistic missile technology, with nearly every rocket stage treated as expendable hardware. The rationale was simple: successfully reaching space was already challenging, so adding recovery mechanisms seemed impractical. Systems like the Saturn V or the Soviet R-7 (which still forms the basis for modern Soyuz launches) were designed for reliability and brute-force capability, not reusability.
NASA’s Space Shuttle program was a partial departure from this expendable approach. Introduced in 1981, the Shuttle orbiter and its two solid rocket boosters were recovered and reused, although the large external tank was expended on each flight. The Shuttle demonstrated that flying hardware multiple times was technically possible but also revealed major pitfalls. High refurbishment costs, extensive inspection requirements, and the delicate nature of thermal protection systems meant that genuine cost savings were elusive.
Still, the Shuttle era proved a crucial stepping stone. Engineers learned about refurbishable rocket engines (the Space Shuttle Main Engines, or SSMEs, each of which could be reused multiple times), aerodynamic reentry, and the complexity of real-time guidance systems. These lessons would influence the next generation of private and government-led efforts to achieve more sustainable—and more profitable—reusability models.
Private Ventures and Breakthrough Milestones
In the early 2000s, new players like SpaceX and Blue Origin entered the launch market, bringing fresh ideas. SpaceX, founded by Elon Musk, set out to build rockets that could do what had been long considered nearly impossible: land on their tails after delivering payloads to orbit. By 2015, the Falcon 9 first stage achieved a historic vertical landing. Not long after, re-flown boosters became routine, proving to skeptics that reusability wasn’t just a gimmick—it was a viable way to cut mission costs.
Meanwhile, Blue Origin, led by Jeff Bezos, followed a suborbital path with New Shepard, which made repeated flights above the Kármán line. Though its missions were shorter than orbital flights, the ability to launch, land, refurbish, and relaunch a rocket multiple times in quick succession demonstrated how a dedicated reusability strategy could work in practice. These efforts fueled a broader shift in the industry: other companies and national space agencies saw the potential for significantly lowered costs and environmental footprints.
Transforming the Economics of Spaceflight
At the heart of all this lies the economics. Building an entire rocket stage from scratch for each launch is hugely expensive. When a company can save the first stage—arguably the most complex and costly part—and simply replace a few components or re-test an engine, the marginal cost of the next launch plummets. This creates a ripple effect: more affordable launches encourage a surge in new satellites, including constellations for broadband internet, Earth observation, and scientific research. For many smaller players, reusability makes space more accessible, spurring fresh ideas and business models.
Additionally, reusing hardware addresses some environmental concerns. Space debris has become a hot topic, especially with the recent boom in satellites populating low Earth orbit. Recovering boosters means less rocket detritus in the ocean, fewer materials wasted, and fewer rocket bodies drifting around in space. In an era where sustainability is increasingly valued, reusability resonates with governments and private stakeholders alike.
Technological Achievements Enabling Reusability
Achieving repeated flights for the same rocket components isn’t just about bringing them home. Each journey entails massive mechanical loads, extreme temperature differentials, and the potential for delicate hardware damage. Below are some of the core achievements that make modern reusability a reality.
Landing, Guidance, and Control
Retropropulsion and VTVL Landings
One of the most visually dramatic feats in spaceflight is the controlled landing of a rocket stage under its own power, known as vertical takeoff, vertical landing (VTVL). The concept is straightforward: after stage separation, the booster flips around, reignites its engines in short bursts (braking burns), and navigates its way down to a landing site—be it a floating platform or a concrete pad.
To pull this off, the rocket uses:
- Grid Fins: Deployed during descent to provide aerodynamic control in varying atmospheric densities.
- Landing Legs: Folded against the rocket’s body during ascent, then deployed in the final seconds for touchdown.
- Engine Gimbaling: Adjusts the thrust vector for pitch, roll, and yaw corrections, acting in concert with aerodynamic surfaces.
This technique is challenging because it demands incredibly precise timing and powerful real-time guidance algorithms. The rocket must monitor altitude, velocity, and wind conditions, constantly updating its descent profile. Any slight deviation in engine thrust or weather patterns can force last-second adjustments.
Advanced Guidance Algorithms and Sensors
Modern rockets integrate data from a suite of sensors: inertial measurement units (IMUs) that track acceleration and rotation, GNSS receivers that provide position and velocity, and radar or laser altimeters measuring height above ground level. These readings feed into a flight computer that executes thousands of calculations per second. If the rocket starts to veer off course, the computer commands quick corrections—either altering engine throttle or adjusting grid fins. Coupled with robust communication links to mission control, the booster can adapt to unexpected variables (like stronger-than-predicted winds) and still stick the landing.
Reusable and Refurbishable Engines
High-End Materials and Manufacturing
Rocket engines for reusable flight must endure repeated ignition cycles without suffering catastrophic wear. This is particularly tough in high-pressure, staged-combustion designs (like SpaceX’s Raptor or Blue Origin’s BE-4). Key material choices include:
- Nickel Superalloys (e.g., Inconel) or advanced copper alloys that hold up under extreme thermal and mechanical stresses.
- 3D-Printed Components that minimize welds and joints—common weak points in complex parts like turbopump housings or combustion chambers.
By using innovative materials and manufacturing methods, companies lower the risk of cracks or erosion, thus enabling multiple flights per engine.
Inspection and Quick Turnaround
Engine reusability isn’t only about surviving flight; it’s also about fast refurbishment. If mechanics need months to strip down a booster or if each engine must be overhauled in detail, the cost advantages diminish. Consequently, firms refine their “post-flight check” routines to include borescope inspections, fluid flushes, and minimal part swaps. Some engines are designed to be opened up like modular kits, making it easier to spot issues and replace just the worn sections.
Structural Lightness and Thermal Management
Composite Structures
To maintain a high payload-to-orbit capability despite carrying landing gear and reserve fuel, rocket builders aim for extremely light structures. Carbon-fiber composites stand out for their strength-to-weight ratio, especially in fairings and tank barrels. Aluminum-lithium alloys, while heavier than carbon composites, offer a cost-effective alternative with proven reliability in cryogenic tank applications.
Reentry Heat and Airstream Loads
During descent, boosters often face a partial reentry environment. While it’s less punishing than what a spacecraft endures returning from orbital speeds, it still includes shock heating and rapid air compression. Some companies rely on:
- Engine-Back Burns to slow down before the denser atmosphere.
- Thermal Coatings or ablative layers over high-heat areas.
- Robust Attachments to secure external hardware (e.g., fins, antennas), preventing them from tearing off in supersonic flow.
Each mission profile is carefully calculated so the rocket never encounters more heat or mechanical load than its protective layers can handle.
Challenges and Opportunities
Reusability unquestionably unlocks new possibilities, but it also reveals fresh hurdles. From balancing performance demands to exploring next-generation concepts, the field is in constant flux. Below, we’ll dissect three main challenge/opportunity areas—and then look at CALLISTO, a European demonstrator that’s part of this growing ecosystem.
Trade-Offs in Payload Capacity
Because landing hardware and extra propellant for the descent add mass, a reusable rocket typically can’t loft as heavy a payload as an expendable variant of the same design. This trade-off leads to strategic decisions:
- Fully Reusable vs. Partially Reusable: Some missions skip booster recovery if they require the rocket’s full performance for heavier payloads (e.g., certain geostationary transfers).
- Customer Priorities: Commercial clients weigh reduced payload mass against cheaper launch costs. For many satellites, the cost benefit of a reusability discount far outweighs the capacity penalty—assuming the satellite’s mass still fits within the rocket’s reusable envelope.
In short, reusability isn’t a one-size-fits-all solution. The mission type, payload mass, and orbit influence whether a rocket flies in reusable mode.
Economic and Environmental Upsides
- Cost Reduction: Every reused booster means one less brand-new booster to build, saving millions in manufacturing.
- Launch Frequency: Lower prices and a more efficient supply chain open the door for frequent flights, fueling satellite constellations, exploration missions, and even tourism.
- Eco-Conscious Approach: Fewer rocket stages ending up on the ocean floor, plus reduced raw materials for new booster production. For agencies aiming at sustainability, reusability addresses part of the “space debris” challenge, too.
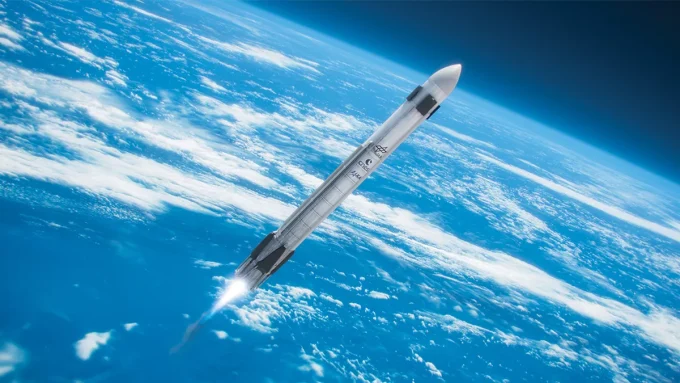
Artist’s view of Callisto © CNES/Orbital Dreams, 2023
A Growing Ecosystem of Reusable Projects
SpaceX has popularized reusability with its Falcon series, notching dozens of successful landings. Blue Origin has made suborbital reusability look routine with New Shepard, while its future New Glenn rocket aims to reuse its gigantic first stage. Rocket Lab is refining partial reuse (catching the Electron booster mid-air via helicopter). Many emerging startups are also toying with reusability in some form—engine recovery, fairing reuse, or second-stage demonstration flights. The widespread interest ensures that reusability will continue evolving rapidly, with unique design philosophies emerging around the world.
CALLISTO: A European Demonstrator Leading the Way
A key European example illustrating the region’s commitment to reusability is the CALLISTO program. Jointly developed by CNES (France), DLR (Germany), and JAXA (Japan), CALLISTO is a small-scale reusable launcher demonstrator designed to test critical technologies for future full-scale rockets.
- Main Objective: Validate autonomous flight, landing maneuvers, and rapid refurbishment protocols in a controlled environment.
- Design Philosophy: CALLISTO’s first stage includes advanced sensors, robust landing gear, and flexible propulsion strategies to handle repeated flights.
- International Collaboration: CNES, DLR, and JAXA share data, resources, and testing facilities, symbolizing how reusability isn’t just a commercial push—it’s also a strategic priority for global space agencies.
If CALLISTO proves its concept, the lessons learned could flow into future European heavy-lift rockets, potentially giving Europe a domestic reusable solution in the mold of Falcon 9 or New Glenn. This synergy between agencies highlights the broader enthusiasm for reusability as a cornerstone of next-gen launch architectures—reducing cost, spurring industrial competitiveness, and lowering environmental impact on a global scale.
The Critical Role of Launcher Antennas
While rocket engines and structure get much of the spotlight, communications and navigation are absolutely vital for reusability. A rocket stage can’t land itself if it “goes dark” mid-flight, and mission control can’t monitor an engine anomaly without a steady data stream. Launcher antennas keep that link alive in every phase: ascent, coasting, reentry, and touchdown.
Telemetry, Tracking, and Command (TT&C)
- Telemetry Downlink: During flight, the rocket constantly streams performance metrics—thrust levels, fuel consumption, structural loads, temperatures, avionics statuses—to ground stations. Engineers and flight controllers rely on this data to see if everything is nominal and to diagnose anomalies in real time.
- Command Uplink: If the rocket needs an in-flight course correction or, in extreme cases, a flight termination command, ground control sends those signals through the same or a parallel frequency band. Without a reliable antenna, these instructions might never reach the vehicle.
For reusable boosters, telemetry and command links remain crucial for post-separation phases. Landing a booster on a drone ship hundreds of kilometers downrange requires near-continuous communication with the stage, sometimes relayed via overhead satellites or dedicated tracking ships.
GNSS for Precision Landings
Large boosters attempting vertical landings rely on accurate positioning. GNSS antennas, usually locked onto multiple constellations (GPS, Galileo, GLONASS, BeiDou), provide position and velocity data that merges with inertial measurements. This combined solution tells the rocket exactly where it is and how fast it’s dropping, enabling the flight computer to plan precise engine burns and alignment angles. Even small GNSS errors—on the order of a few meters—can mean missing a landing platform entirely or tipping over upon touchdown.
Environmental Stresses on Antennas
Rockets experience extreme conditions:
- High G-Loads: Liftoff thrust can exceed 4–5 g, plus abrupt staging events create shock waves that can damage unreinforced components.
- Temperature Swings: A booster can go from near sea-level warmth to the cold vacuum of near-space in minutes, then heat up again during reentry.
- Aerodynamic Forces: Descending at supersonic speeds subjects external antenna housings (radomes) to punishing airflow, risking vibration or tearing if not properly designed.
Consequently, launcher antennas must be rugged, thermally protected, and firmly mounted. They’re typically tested under intense vibration tables and thermal cycling labs to ensure reliable performance across the entire mission.
Anywaves Launcher Antennas
In order to address the needs of reusable launchers market, Anywaves has developed a new range of rocket antennas, specifically designed to withstand the harsh conditions faced by launchers.
By focusing on launcher-specific constraints, these antennas help maintain reliable communications and navigation throughout ascent, staging, and landing, thereby bolstering the rocket’s chances of a successful re-flight.
Conclusion
The reusable rocket revolution is reshaping how we get to space. Instead of discarding advanced hardware after a single flight, companies and agencies are showing that boosters, engines, fairings, and other critical components can be reclaimed, refurbished, and relaunched. This shift lowers costs, increases flight frequency, and limits environmental impact—a trifecta of benefits that was once considered too good to be true.
Yet pulling it off demands a holistic approach. Designers must integrate robust landing systems, carefully chosen materials, and thorough post-flight inspections. The engine team has to ensure each turbine blade and chamber lining can survive multiple ignitions. Ground operations must pivot from full rebuilds to swift checkouts, all while balancing mission schedules. And at the core of it all, reliable launcher antennas transmit vital data and navigation signals that allow the rocket to execute precision landings.
Whether through the dramatic tail landings popularized by SpaceX, helicopter snags attempted by Rocket Lab, or suborbital hops with Blue Origin, the principle remains the same: if you can safely recover hardware, you can reuse it, save money, and fly more often. Demonstrators like Europe’s CALLISTO are broadening these possibilities further, combining international expertise to develop next-generation flight profiles and refurbishment strategies.
In an industry where every kilogram counts and reliability is paramount, reusability signals a transformative leap. It’s no longer a novelty—it’s rapidly becoming the baseline for new launch systems around the world. The result? A more accessible, dynamic, and sustainable space sector, where robust antennas, thrifty engines, and advanced structures all play an essential role in ensuring that what goes up can come back down and fly again.
Contact
us
If you have any question, we would be happy to help you out.